When it comes to copyright law and the application of fair use exceptions, ignorance is definitely not bliss! Learn how to educate yourselves and your students and avoid making a costly mistake!
You really did plan to find time over the summer to familiarize yourself with the latest information on copyright law. You absolutely intended to look up the fair use guidelines for using technology resources. You truly meant to create a classroom copyright policy, locate agencies that grant permissions to use copyrighted materials, write a template for a permission request form, and locate sites to teach students about the value of original work and the societal benefits of obeying copyright laws. You just had a few other things to do.
So now you have a student who wants to include audio of a Beatles song in a multimedia presentation about the 1960s, another who wants to include the poem "Casey at the Bat" in a report on the World Series, and a third who wants to post photographs of Biden and Obama to the class Web site.
What's an educator to do? Read Education World's five-part series on copyright, fair use, and new technologies, that's what! We did the work so you wouldn't have to!
Source: http://www.educationworld.com/a_curr/curr280.shtml
จำนวนการดูหน้าเว็บรวม
วันพุธที่ 15 กุมภาพันธ์ พ.ศ. 2555
Chapter 12 Knowledge Management
Samsung Electronics’ Knowledge Management System
In April, 2009 the Visual Display Division of Samsung Electronics' Digital Media Business had just completed work on a ground breaking high-resolution LED TV. The company was vigorously engaged in a massive campaign to announce this remarkable product, which was expected to take the global TV market by storm. The Visual Display Division was poised to take a well deserved breather from the marathon development and production phases of this landmark project and take a moment to bask in the glory of their achievement. Shortly, they came to understand why it is often said that no good deed goes unpunished. The Division was blindsided by the call to initiate a new mission. Samsung management issued an edict: The Visual Display Division will roll out full-HD 3DTV within a year. There was no time to waste resting on their laurels, it was time for the division to get cracking .... again.
Korea's Hyundai IT had developed a 3DTV in 2007 and Sony was making systemic preparations to beat Samsung Electronics to the market with a 3DTV of their own. There was little doubt that Samsung Electronics was playing catch-up. The best and the brightest of relevant departments were assembled to staff the new mission. Two task forces, identified as C7000 and C8000, were immediately established. The task forces dusted off the results of studies on 3D that were conducted over the past several years and began to give them a fresh look.
At this time Samsung Electronics’ knowledge management system (KMS), called the Test and Error Management System, or TEMS, was called upon to play a key role in the project. TEMS, which is known by Samsung electronics engineers as the "treasure chest", contains all information related to each step of Samsung Electronics' product development. The one-year process of developing 3DTV is also enshrined in TEMS, as is to be expected. In fact, in addition to the stellar efforts of the highly committed team in the Visual Display Division, it was Samsung Electronics’ knowledge management system that was responsible for closing the gulf between them and their rivals and making it happen in just one year.
In his book, Management Challenges for the 21st Century, Peter Drucker noted "The 21st century is a knowledge-based society, where knowledge workers are the most important factor of production. In other words, conventional economics' production factors, the 4Ms - Man, Machine, Material and Method - will be replaced by workers armed with knowledge. Thus, management of knowledge workers will form the foundation of corporate management."
As the technology of TV has evolved to deliver HD 3DTV, so has the methodology of producing world-class products and maintaining a competitive advantage in the global marketplace. Samsung demonstrated in practice what Drucker proposed in this book, that by leveraging the value of their KMS, they were able to achieve the goal of HD 3DTV in a year. This is a fact that is surely not lost on their rivals.
Source:http://www.koreaittimes.com/story/10828/samsung-electronics%E2%80%99-knowledge-management-system
Korea's Hyundai IT had developed a 3DTV in 2007 and Sony was making systemic preparations to beat Samsung Electronics to the market with a 3DTV of their own. There was little doubt that Samsung Electronics was playing catch-up. The best and the brightest of relevant departments were assembled to staff the new mission. Two task forces, identified as C7000 and C8000, were immediately established. The task forces dusted off the results of studies on 3D that were conducted over the past several years and began to give them a fresh look.
At this time Samsung Electronics’ knowledge management system (KMS), called the Test and Error Management System, or TEMS, was called upon to play a key role in the project. TEMS, which is known by Samsung electronics engineers as the "treasure chest", contains all information related to each step of Samsung Electronics' product development. The one-year process of developing 3DTV is also enshrined in TEMS, as is to be expected. In fact, in addition to the stellar efforts of the highly committed team in the Visual Display Division, it was Samsung Electronics’ knowledge management system that was responsible for closing the gulf between them and their rivals and making it happen in just one year.
In his book, Management Challenges for the 21st Century, Peter Drucker noted "The 21st century is a knowledge-based society, where knowledge workers are the most important factor of production. In other words, conventional economics' production factors, the 4Ms - Man, Machine, Material and Method - will be replaced by workers armed with knowledge. Thus, management of knowledge workers will form the foundation of corporate management."
As the technology of TV has evolved to deliver HD 3DTV, so has the methodology of producing world-class products and maintaining a competitive advantage in the global marketplace. Samsung demonstrated in practice what Drucker proposed in this book, that by leveraging the value of their KMS, they were able to achieve the goal of HD 3DTV in a year. This is a fact that is surely not lost on their rivals.
Source:http://www.koreaittimes.com/story/10828/samsung-electronics%E2%80%99-knowledge-management-system
วันจันทร์ที่ 6 กุมภาพันธ์ พ.ศ. 2555
Chapter 11
Toyota is all about the customer. We hear a lot — and I’ve written a lot on this blog — about the Toyota Production System, anglicized in the United States as Lean, but we haven’t known much about the role of Information Technology at Toyota.
Baseline Magazine has a great article on Toyota; specifically, the role of technology at Toyota1:
And behind TPS is information technology—supporting and enabling the business processes that help Toyota eliminate waste, operate with virtually no inventory and continually improve production.
Technology does not drive business processes at Toyota. The Toyota Production System does. However, technology plays a critical role by supporting, enabling and bringing to life on a mass scale the processes derived by adhering to TPS.
And more,
Over the years, Toyota refined a number of other concepts and production methods that support the two central TPS pillars. And behind each of those pillars are information systems, supporting and enabling the processes:
Just-in-time: Toyota employs one of the most sophisticated supply chain systems in manufacturing, working closely with suppliers to ensure that parts arrive just when needed. For example, when a car comes out of the paint shop in Georgetown, the system sends seat supplier Johnson Controls an electronic message detailing the exact configuration of the seats required (leather upholstery, bucket seats, etc.); Johnson Controls has four hours to ship those seats to the plant in the exact sequence required. The instructions are provided by Toyota’s proprietary Assembly Line Control System (ALCS) software.
Jidoka: At every stage of the assembly line, Toyota employs devices allowing workers to stop production to correct defects. Such devices may be as simple as a rope strung above the assembly line, or a button that can be pushed. In other cases, it is sophisticated monitoring software such as Activplant’s Performance Management System, which can alert operators to problems with equipment or robots in real time.
Kaizen: This is a system for continuous improvement. Toyota constantly looks to improve its business processes by finding ways to take Muda (waste) out of the system. It can be as simple as moving a tool to an assembly station so a worker does not need to waste time walking to get the tool. Or it may involve technology, such as allowing dealerships to swap car inventories using the Dealer Daily, an Internet portal, so customers are not left waiting longer for the vehicle they want.
Andon: Wherever possible, Toyota uses visual controls, or Andons, such as overhead displays, plasma screens and electronic dashboards to quickly convey the state of work. On the assembly line floor, for example, overhead Andons tell a supervisor with one glance whether the station is functioning smoothly (a green light), whether there is a problem being investigated (yellow light) or whether the assembly line has stopped (red light). Newer plasma screens, tied into assembly line equipment, provide even more information such as which machine malfunctioned, the operator and the exact conditions (speed, temperature) when it broke down.
Poka Yoke: Toyota uses a range of these low-cost, highly reliable devices throughout its operations to prevent defects. A PokaYoke may be something as simple as a tool holder with an electronic sensor, or it may be a light curtain, a beam of light that sends a signal to a computer when a hand or some other object interrupts its flow. The curtain can signal a warning if, for instance, a worker fails to pick up a cotter pin, bolt, nut or some other required part.
Genchi Genbutsu: The literal translation of this term is, “Go and see for yourself.” Rather than hear about a problem, Toyota requires its workers, team leaders and executives to go and see a problem directly and to work collectively on a solution. At least 50% of Toyota’s information systems workers are stationed at plant sites to work directly with operations.
A case in point in how technology supports TPS and the customer:
In all, the Dealer Daily [Toyota's application for car dealers] incorporates more than 120 business applications, and like all Toyota initiatives, it is constantly undergoing Kaizen to look for more improvements and opportunities to remove Muda. Case in point: Toyota recently added the capability for dealers to find out which vehicles it has in the production pipeline, and make changes such as switching a cloth interior to leather. (Dealer Daily is integrated into Toyota’s mainframe systems through file transfer protocol and System Network Architecture [SNA], IBM’s proprietary networking architecture, although Web services are now being explored.) By logging in the next day, the dealer can find out if the changes were received in time and accepted. This allows the dealers to more closely customize orders to actual customer demand.
Here’s a look at the current proprietary technologies at Toyota, all modified to support the business:
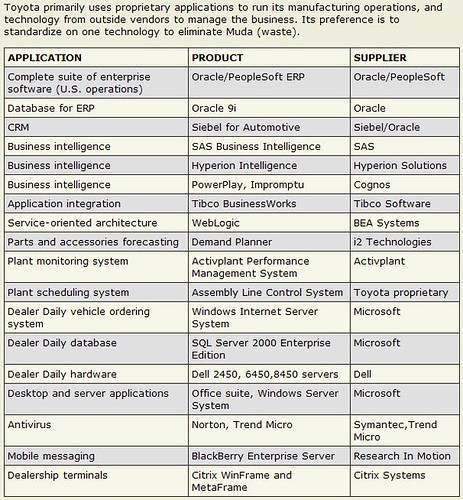
Source: http://www.shmula.com/information-technology-at-toyota/205/
Baseline Magazine has a great article on Toyota; specifically, the role of technology at Toyota1:
And behind TPS is information technology—supporting and enabling the business processes that help Toyota eliminate waste, operate with virtually no inventory and continually improve production.
Technology does not drive business processes at Toyota. The Toyota Production System does. However, technology plays a critical role by supporting, enabling and bringing to life on a mass scale the processes derived by adhering to TPS.
And more,
Over the years, Toyota refined a number of other concepts and production methods that support the two central TPS pillars. And behind each of those pillars are information systems, supporting and enabling the processes:
Just-in-time: Toyota employs one of the most sophisticated supply chain systems in manufacturing, working closely with suppliers to ensure that parts arrive just when needed. For example, when a car comes out of the paint shop in Georgetown, the system sends seat supplier Johnson Controls an electronic message detailing the exact configuration of the seats required (leather upholstery, bucket seats, etc.); Johnson Controls has four hours to ship those seats to the plant in the exact sequence required. The instructions are provided by Toyota’s proprietary Assembly Line Control System (ALCS) software.
Jidoka: At every stage of the assembly line, Toyota employs devices allowing workers to stop production to correct defects. Such devices may be as simple as a rope strung above the assembly line, or a button that can be pushed. In other cases, it is sophisticated monitoring software such as Activplant’s Performance Management System, which can alert operators to problems with equipment or robots in real time.
Kaizen: This is a system for continuous improvement. Toyota constantly looks to improve its business processes by finding ways to take Muda (waste) out of the system. It can be as simple as moving a tool to an assembly station so a worker does not need to waste time walking to get the tool. Or it may involve technology, such as allowing dealerships to swap car inventories using the Dealer Daily, an Internet portal, so customers are not left waiting longer for the vehicle they want.
Andon: Wherever possible, Toyota uses visual controls, or Andons, such as overhead displays, plasma screens and electronic dashboards to quickly convey the state of work. On the assembly line floor, for example, overhead Andons tell a supervisor with one glance whether the station is functioning smoothly (a green light), whether there is a problem being investigated (yellow light) or whether the assembly line has stopped (red light). Newer plasma screens, tied into assembly line equipment, provide even more information such as which machine malfunctioned, the operator and the exact conditions (speed, temperature) when it broke down.
Poka Yoke: Toyota uses a range of these low-cost, highly reliable devices throughout its operations to prevent defects. A PokaYoke may be something as simple as a tool holder with an electronic sensor, or it may be a light curtain, a beam of light that sends a signal to a computer when a hand or some other object interrupts its flow. The curtain can signal a warning if, for instance, a worker fails to pick up a cotter pin, bolt, nut or some other required part.
Genchi Genbutsu: The literal translation of this term is, “Go and see for yourself.” Rather than hear about a problem, Toyota requires its workers, team leaders and executives to go and see a problem directly and to work collectively on a solution. At least 50% of Toyota’s information systems workers are stationed at plant sites to work directly with operations.
A case in point in how technology supports TPS and the customer:
In all, the Dealer Daily [Toyota's application for car dealers] incorporates more than 120 business applications, and like all Toyota initiatives, it is constantly undergoing Kaizen to look for more improvements and opportunities to remove Muda. Case in point: Toyota recently added the capability for dealers to find out which vehicles it has in the production pipeline, and make changes such as switching a cloth interior to leather. (Dealer Daily is integrated into Toyota’s mainframe systems through file transfer protocol and System Network Architecture [SNA], IBM’s proprietary networking architecture, although Web services are now being explored.) By logging in the next day, the dealer can find out if the changes were received in time and accepted. This allows the dealers to more closely customize orders to actual customer demand.
Here’s a look at the current proprietary technologies at Toyota, all modified to support the business:
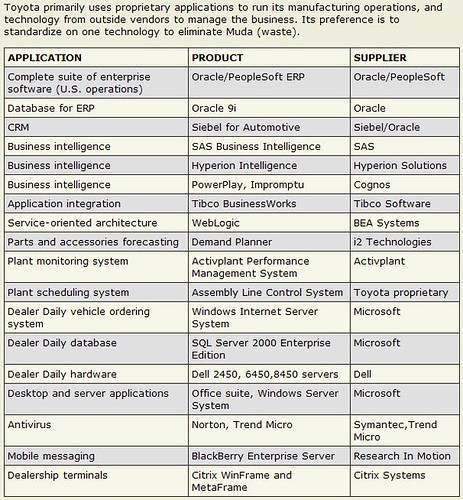
Source: http://www.shmula.com/information-technology-at-toyota/205/
สมัครสมาชิก:
บทความ (Atom)